What is Porosity in Welding: Secret Aspects and Their Effect On Weld Quality
What is Porosity in Welding: Secret Aspects and Their Effect On Weld Quality
Blog Article
Porosity in Welding: Identifying Common Issues and Implementing Ideal Practices for Prevention
Porosity in welding is a prevalent problem that typically goes unnoticed till it causes substantial problems with the stability of welds. In this discussion, we will certainly check out the key aspects adding to porosity formation, analyze its harmful results on weld efficiency, and go over the best practices that can be adopted to reduce porosity event in welding processes.
Typical Reasons For Porosity
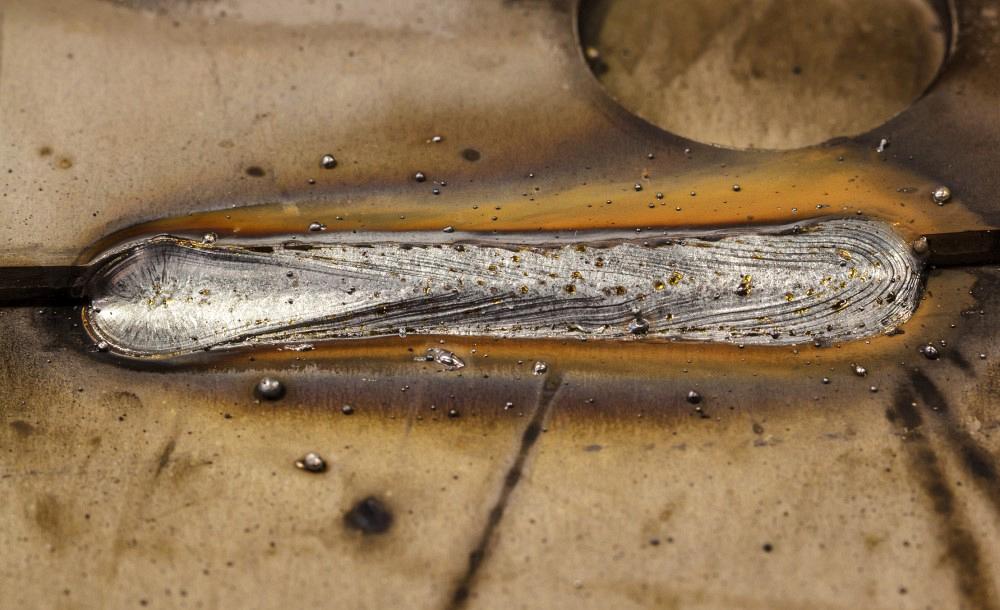
Making use of dirty or wet filler products can introduce pollutants right into the weld, contributing to porosity problems. To mitigate these typical reasons of porosity, comprehensive cleansing of base metals, appropriate protecting gas option, and adherence to optimum welding specifications are vital techniques in achieving top quality, porosity-free welds.
Influence of Porosity on Weld Quality

The presence of porosity in welding can dramatically jeopardize the structural honesty and mechanical buildings of welded joints. Porosity produces voids within the weld metal, weakening its overall stamina and load-bearing capacity.
Welds with high porosity degrees often tend to display lower impact strength and minimized ability to warp plastically prior to fracturing. Porosity can restrain the weld's capacity to properly transmit forces, leading to premature weld failure and prospective safety hazards in important frameworks.
Best Practices for Porosity Prevention
To improve the structural honesty and high quality of welded joints, what certain measures can be applied to minimize the occurrence of porosity during the welding procedure? Porosity avoidance in welding is important to ensure the integrity and stamina of the final weld. One reliable method appertains cleansing of the base steel, removing any type of pollutants such as corrosion, oil, paint, or dampness that might bring about gas entrapment. Ensuring that the welding equipment is in excellent problem, with clean consumables and suitable gas circulation prices, read what he said can also substantially decrease porosity. Additionally, keeping a stable arc and controlling the welding parameters, such as voltage, current, and travel speed, aids produce a regular weld swimming pool that reduces the danger of gas entrapment. Making use of the proper welding method for the certain product being bonded, such as readjusting the welding angle and weapon placement, can further avoid porosity. Regular evaluation of welds and instant removal of any concerns recognized throughout the welding process are important methods to prevent porosity and produce top quality welds.
Relevance of Correct Welding Methods
Implementing proper welding techniques is paramount in guaranteeing the architectural stability and high quality of bonded joints, building upon the structure of effective porosity prevention measures. Extreme heat can lead to increased porosity due to the entrapment of gases in the weld swimming pool. Additionally, utilizing the appropriate welding criteria, such as voltage, present, and travel rate, is essential for attaining audio welds with marginal porosity.
Moreover, the selection of welding procedure, whether it be MIG, TIG, or stick welding, ought to line up with the particular needs of the task to guarantee ideal results. Appropriate cleaning and prep work of check this the base steel, as well as picking the ideal filler material, are also important elements of efficient welding strategies. By adhering to these best practices, welders can lessen the risk of porosity formation and create top quality, structurally sound welds.
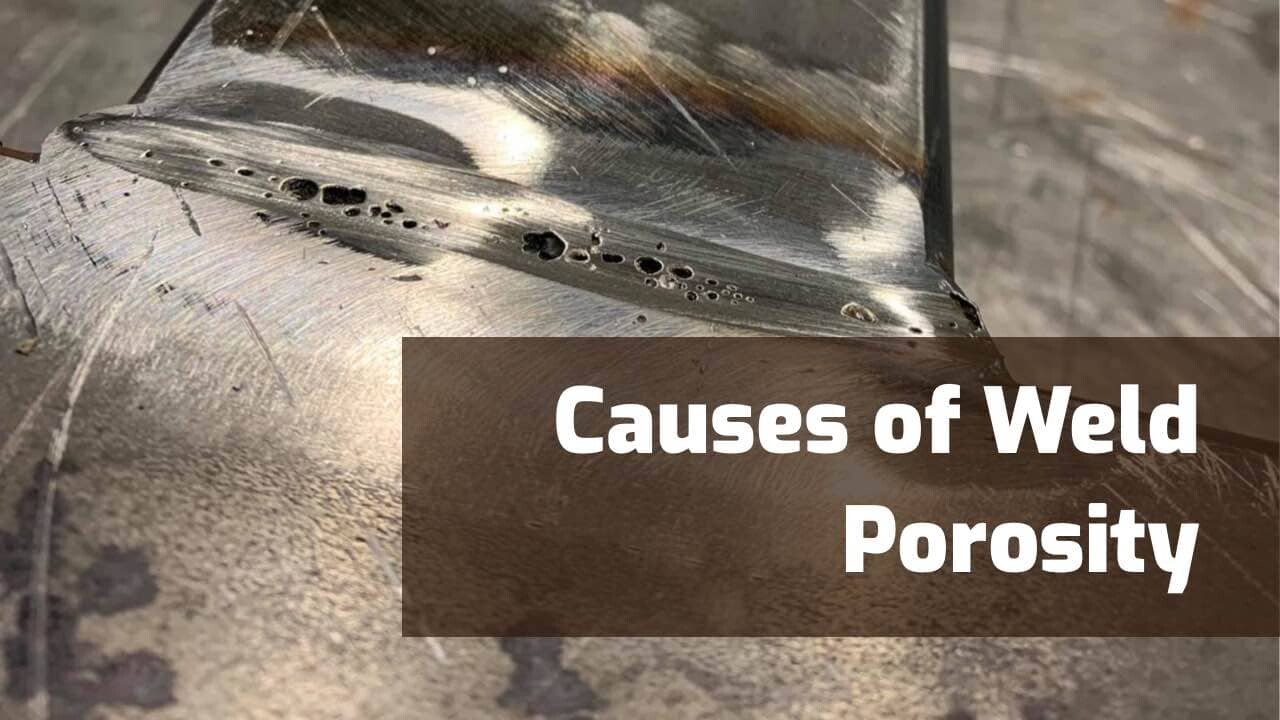
Examining and Quality Assurance Measures
Quality control steps play a crucial function in verifying the honesty and integrity of welded joints. Examining treatments are vital to detect and protect against porosity in welding, making certain the toughness and toughness of the final product. Non-destructive testing techniques such as ultrasonic testing, radiographic testing, and aesthetic evaluation are generally employed to recognize possible issues like porosity. These strategies permit the assessment of weld Get More Info high quality without compromising the stability of the joint. What is Porosity.
Post-weld inspections, on the various other hand, assess the final weld for any type of issues, including porosity, and validate that it meets defined criteria. Carrying out a detailed quality control strategy that consists of detailed testing treatments and evaluations is vital to minimizing porosity concerns and making sure the general high quality of welded joints.
Verdict
In conclusion, porosity in welding can be a common problem that affects the quality of welds. By identifying the usual reasons for porosity and executing best techniques for avoidance, such as proper welding strategies and screening steps, welders can ensure high top quality and reputable welds. It is vital to focus on avoidance approaches to reduce the incident of porosity and preserve the honesty of bonded structures.
Report this page